75 anni di tecnologia di compoundazione continua
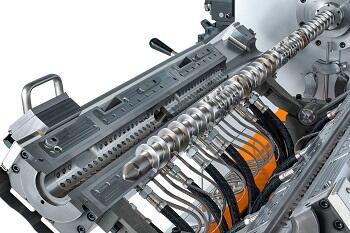
Ha da poco compiuto 75 anni la tecnologia di Buss per la compoundazione delicata ed efficiente allo stesso tempo. Era infatti il 20 agosto 1945 quando l’ingegnere Heinz List depositava una domanda di brevetto per il principio costruttivo alla base del sistema di compoundazione continua da lui inventato, segnando così la nascita di tale tecnologia. Buss, convinta del suo potenziale, inaugurò nel 1948 il primo centro di collaudo per sistemi di compoundazione continua e nel 1950, dopo che List aveva nel frattempo assunto il ruolo di direttore tecnico dell’azienda, iniziavano le consegne dei primi sistemi per la lavorazione di PVC e polistirene.
Da allora, sono stati costruiti otre 3500 sistemi, fornendo in più di 80 paesi del mondo soluzioni personalizzate in base alle esigenze specifiche di compoundatori e applicazioni. Queste ultime spaziano dalla lavorazione dei tecnopolimeri ad alte prestazioni con cariche sensibili alle alte temperature o al taglio, quali il nerofumo conduttivo (in concentrazioni anche superiori al 90%), alla produzione di formulazioni per le industrie dell’alluminio, chimica e alimentare. Il portafoglio di sistemi di compoundazione di Buss nel campo delle materie plastiche e degli elastomeri comprende attualmente la serie Compeo, disponibile in sei modelli in grado di raggiungere una produttività di 12800 kg all’ora nella lavorazione dei materiali termoplastici.
Un principio di funzionamento speciale
L’azione miscelante, altamente efficiente e al contempo delicata, è il frutto dello speciale principio di funzionamento del sistema di compoundazione continua. Da un lato, la filettatura della vite si interrompe in due-quattro punti a ogni giro; in questi punti intervengono le caratteristiche alette che vanno a interagire con i perni infissi nell’alloggiamento del sistema di compoundazione. Inoltre, l’albero della vite esegue un movimento di rotazione e, contemporaneamente, di oscillazione assiale, compiendo a ogni giro una corsa completa in avanti per poi tornare alla posizione di partenza.
La forza di taglio necessaria per la fusione e la dispersione si genera nell’area di taglio tra aletta e perno. Grazie a questo particolare design, la velocità di taglio non dipende dalle dimensioni della macchina, bensì risulta direttamente proporzionale alla velocità di rotazione dell’albero della vite. Ne consegue, come ulteriore vantaggio della tecnologia di compoundazione continua, un’agevole scalabilità del sistema, dal modello di laboratorio alla versione per le produzioni di serie.
Una varietà di applicazioni sempre più ampia
Per molti utilizzatori impegnati a produrre una gamma diversificata di articoli, il sistema rappresenta una scelta privilegiata in virtù delle sue numerose qualità, oltre a essersi imposta come la tecnologia predominante in alcuni segmenti di nicchia. I produttori di sistemi isolanti per cavi a media e alta tensione, ad esempio, beneficiano soprattutto della termoregolazione ad alta precisione in sede di estrusione reattiva. Nel segmento dei compound semiconduttori invece il vantaggio è rappresentato dalla distribuzione delicata degli additivi, mentre per altri materiali termoplastici è la lavorazione entro finestre di processo ristrette a svolgere un ruolo decisivo.
Tra le applicazioni in ambito medicale vi è la produzione di compound utilizzati nei sistemi di movimentazione di liquidi e per il confezionamento sterile dei farmaci, di compound con effetti antibatterici e antivirali e degli adesivi, ad esempio, usati nei materiali per fasciature. Grazie alle velocità di taglio contenute e alle buone caratteristiche di miscelazione, il sistema consente, in questo ambito, la diffusione omogenea di quantità di additivi anche molto ridotte.
Nelle applicazioni in cui un ruolo importante è svolto dagli additivi sensibili alla temperatura e/o al taglio, ad esempio in presenza di compound a base di PBT o di PA resistente alle alte temperature, materiali termoindurenti la cui compoundazione deve essere eseguita al di sotto della temperatura di reticolazione, o materiali rinforzati con fibre naturali, le velocità di taglio contenute consentono una lavorazione entro finestre di processo ristrette. Le produzioni, in questo caso, spaziano dai componenti elettronici alle parti destinate al vano motore, fino alle strutture leggere utilizzate nelle automobili e nei velivoli.