La macchina perfetta per soluzioni complesse
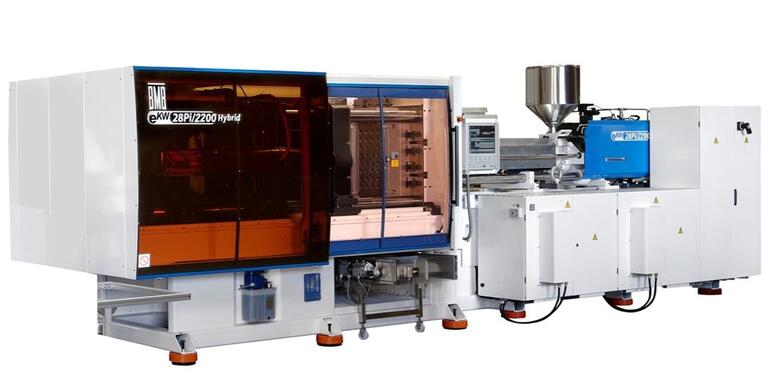

Spesso BMB viene identificata come una macchina costosa finalizzata alle alte velocità. Di seguito una recente esperienza vissuta con un nostro importante cliente a dimostrazione che non è certo solo questo. Un importante brand del settore degli elettrodomestici ha lanciato una sfida ai propri fornitori per raggiungere la produzione ottimale del nuovo cassetto per il detersivo delle lavatrici, denominato tecnicamente “Vortex” dalla casa dell’elettrodomestico.
La grande casa di elettrodomestici chiede ai propri fornitori standard elevatissimi, massima qualità del prodotto finito, zero scarti ed elevata economicità. Per produrre in Italia un articolo così complesso e articolato, costituito da ben sette o nove pezzi stampati, assemblati tra loro, servono presse di elevata precisione, alte prestazioni in termini di ciclo e affidabilità, contemporaneamente orchestrate da un sistema di automazione che le possa far interagire per ottenere il prodotto finito, senza presidio.

BMB e PLAST GROUP di Fontanelle (Treviso) hanno speso molto tempo a disegnare la disposizione ideale della grande isola di lavoro delle cinque presse coinvolte, passando da una configurazione con stampi a due impronte per poi prendere la strada della maggior semplificazione possibile, con stampi a una impronta e l’obiettivo tassativo di un pezzo finito e controllato ogni 40 secondi.
Il Vortex è costituito da sei pezzi stampati principali, di cui due di essi devono essere saldati tra loro a ultrasuoni prima dell’assiemaggio con gli altri; a questo insieme, a seconda della destinazione del prodotto finale, possono essere integrati altri tre piccoli pezzi di diverso colore provenienti dall’esterno e inseriti dopo la produzione. PLAST GROUP ha coinvolto per il progetto il comparto di automazione interno che, insieme ai tecnici BMB, ha realizzato l’isola di lavoro in perfetta ergonomicità di layout e rispetto degli standard dettati da Industria 4.0.

Le presse coinvolte nell’isola di lavoro sono cinque, tutte della serie Hybrid per garantire le massime prestazioni in termini di ciclo (in alcuni casi sono risultate fondamentali le caratteristiche di elevata velocità di iniezione per il riempimento di pareti sottili, quindi elevate pressioni specifiche, tipiche della serie Hybrid). I due pezzi che successivamente saranno coinvolti nella distribuzione dell’acqua sul detergente devono essere saldati perfettamente tra loro e la serpentina al loro interno deve risultare a tenuta stagna per l’acqua; in questo caso, uno stampo a 1+1 cavità montato su una pressa Hybrid da 450 tonnellate ci darà la possibilità di estrarre i due pezzi, saldarli ad ultrasuoni immediatamente dopo lo stampaggio, quindi sempre con lo stesso robot a sei assi, gestirne i vari spostamenti, per controllo di tenuta dopo ogni accoppiamento e successivo deposito sulla linea che conduce l’assieme alla stazione centrale.
Gli atri quattro componenti principali per l’assemblaggio del cassetto lavatrice, meglio noto tecnicamente con il nome di Vortex, vengono stampati con altre quattro presse della serie Hybrid, rispettivamente da 380, 250, 200 e 160 tonnellate, mentre un’ultima pressa full electric da 160 tonnellate, esterna all’isola di lavoro, si occupa di asservire la linea dei piccoli componenti da inserire a seconda della destinazione finale del prodotto. Ora immaginiamo un quadrato con le due presse più grandi affiancate su un lato e di fronte a esse le tre presse più piccole affiancate anche’esse tra loro. Ognuna di queste presse vedrà confluire verso il centro del quadrato il prodotto da essa stampato; nell’area centrale, tre robot antropomorfi a sei assi, perfettamente interconnessi, si occupano dell’assemblaggio dei pezzi e delle prove di corretto funzionamento di estrazione del “cassetto” a forza controllata, quindi di un controllo visivo, ma contemporaneamente funzionale dell’assieme “abbottonato”, prima della cessione all’unico operatore presente per un ultimo sguardo prima di chiuderlo in una pellicola protettiva e depositarlo nel contenitore per la destinazione finale di assemblaggio della lavatrice.
Vogliamo ringraziare tutto team di PLAST GROUP (www.plastgroupsrl.com) e Gilbero Rui in particolare per averci dato la possibilità di condividere la realizzazione di questo ambizioso progetto realizzato in Italia, certi di poter affiancare nuovamente PLAST in nuove sfide che la vedranno coinvolta in progetti chiavi in mano per i più grandi player dell’elettrodomestico e dell’automotive.
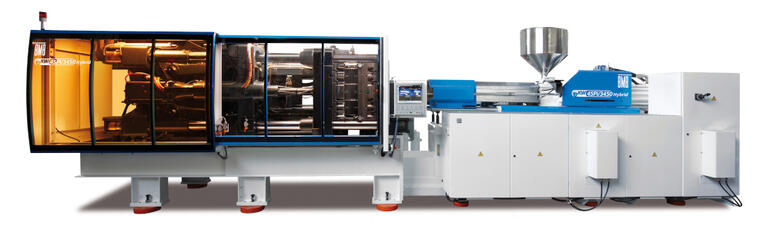