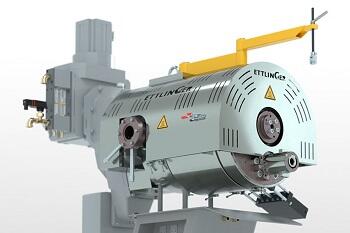
Flakes obtained from plastic waste by grinding can be processed directly in the injection moulding process if any foreign substances are thoroughly removed from the melt. The associated technology was developed by injection moulding machine manufacturer Engel, which chose a high-performance melt filter from Ettlinger, a manufacturer belonging to the Maag Group. This continuously ensures the required purity and thus enables consistent product quality at a high level of production efficiency. The elimination of a separate pelletizing step conserves material and reduces energy requirements and CO2 emissions, contributing to even greater sustainability in the recycling of plastics.
The heart of the innovative, two-stage technology, which Engel will be presenting live for the first time at the K 2022 trade fair, is a modular injection moulding machine from the duo series, designed for the two-stage process. The ERF350 melt filter from Ettlinger, like the additional degassing unit, is positioned between the plasticizing unit and the separate injection unit. Engel decided to integrate this filter because of its ability to continuously and reliably separate solid and elastomeric contaminants from the plastic melt at contamination levels of up to 16%. It operates on a self-cleaning basis, using a rotating, perforated drum, through which there is a flow of melt from the outside to the inside. As it rotates, a scraper removes the contaminants that are held back on the surface and diverts them to the discharge system. This grants the user fully automatic and uninterrupted long-term operation with excellent mixing and homogenization of the melt.
Visitors to K 2022 can experience the use of the ERF350 live at the Engel booth in the Circular Economy Forum. A mixture of post-industrial polyolefins is used there to produce rollable logistics load carriers known as dolly pallets - large-volume moulded parts of the kind often made from recycled materials.