Non c'è auto elettrica senza plastica
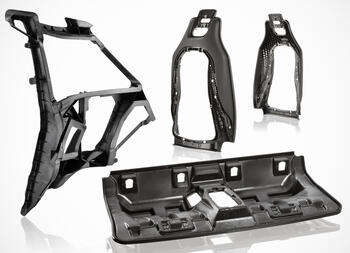
Grazie alla loro versatilità applicativa, i materiali di Basf sono stati scelti da BMW per la realizzazione di svariati componenti della sua vettura elettrica i3. A cominciare dagli schienali dei sedili anteriori, dalle parti di rinforzo della struttura in fibra di carbonio e dal guscio del sedile posteriore.
Lo schienale dei sedili anteriori rappresenta il primo componente strutturale in poliammide stampato a iniezione e senza rivestimento. È realizzato in PA 6 Ultramid B3ZG8 UV a elevata resistenza ai raggi UV, che assicura rigidità, livelli adeguati di allungamento e resistenza a temperature tra -30 e 80°C. Alcuni suoi componenti, invece, sono realizzati in PA 6 Ultramid Structure B3WG8 LG, rinforzata con fibre lunghe di vetro. Per ottenere la sua forma complessa e molto sottile, inoltre, è stato utilizzato il software di simulazione Ultrasim, sviluppato dalla stessa Basf.
La struttura in carbonio contiene elementi portanti in PBT Ultradur B4040 G6. Quello più grande, nonché il primo nel suo genere, si trova nella zona posteriore tra i due gusci strutturali in fibra di carbonio. Oltre a una funzione portante in caso di collisione, li tiene separati e forma l'apertura posteriore per il finestrino laterale. Tale materiale risulta ideale per questa funzione, grazie alla stabilità dimensionale, indipendente dalle condizioni climatiche, e alla resistenza allo schiacciamento. Oltre due dozzine di elementi più piccoli in Ultradur, per un peso complessivo di circa 9 chili, sono integrate in altre aree della struttura come rinforzo e per migliorarne l'isolamento acustico.
Il guscio autoportante del sedile posteriore è ottenuto in poliuretano Elastolit rinforzato con fibre di carbonio. Il componente integra una serie di funzioni, richiede meno tempo per il montaggio e risulta più leggero. Il poliuretano utilizzato si contraddistingue per elevata resistenza alla fatica e al danneggiamento e la parte soggetta a eventuali collisioni soddisfa i severi requisiti di sicurezza imposti dal costruttore, nonostante lo spessore di appena 1,4 mm.
L'espanso strutturale in poliuretano Elastolit D, invece, è utilizzato come materiale di rinforzo del telaio del tettuccio. Altamente resistente alla pressione viene impiegato in una struttura sandwich in carbonio, che garantisce la rigidità strutturale del veicolo.
La i3 integra molti particolari in materiali plastici già utilizzati in numerosi altri veicoli:
- la scatola dei fusibili è in Ultramid B3ZG3, che soddisfa i severi parametri di rigidità e di resistenza alla trazione, un connettore ad alta tensione è in Ultramid A3EG6, mentre guaine per cavi e passacavi sono in poliuretano Elastollan ed Elastoflex
- la retro schiumatura della plancia viene effettuata con l'espanso semirigido in poliuretano Elastoflex E
- l’espanso in poliuretano Elastoflex E è impiegato anche nel tettuccio, come materiale di base di un sandwich composito con eccellente termoformabilità ed elevata rigidità e per migliorarne l'isolamento acustico
- i moduli del tettuccio scorrevole sono in Elastolit R 8919 con incapsulamento di fibre di vetro, resistente a raggi UV e agenti atmosferici, mentre il suo telaio è in Ultradur B 4040 G6, una miscela PBT/PET a ridotta deformabilità
- le sospensioni degli assi anteriore e posteriore sono in Cellasto, elastomero speciale microcellulare.
Infine, la divisione Coatings ha fornito gli strati di fondo in quattro colori per la verniciatura, che soddisfano i requisiti di rivestimento dei componenti aggiuntivi e dei processi interessati.