Tappi tethered: a Plast 2023 Gefit c’è
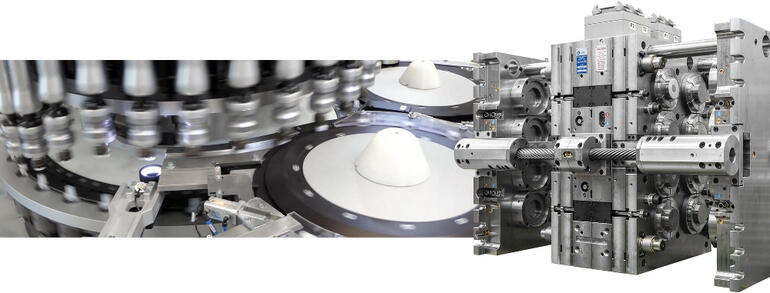
A Plast 2023 Gefit si presenta con le ultime soluzioni sviluppate sia per le macchine sia per gli stampi secondo quanto previsto dalla Direttiva europea UE 904/2019, che entrerà in vigore a luglio 2024 e imporrà l’adozione di tappi e chiusure tethered per bottiglie e contenitori allo scopo di ridurre la dispersione di plastica nell’ambiente.
A tale riguardo, le “slitting machine” con orientamento angolare per prodotti tethered sono state sviluppate per vincolare il tappo alla bottiglia ma allo stesso tempo fare in modo che ciò non interferisca con il versamento della bevanda. L’azienda ha studiato e progettato chiusure tethered orientate di ultima generazione con un particolare finecorsa nel TE che impedisce la rotazione in una posizione indesiderata; la tecnologia Gefit va oltre le attuali macchine da taglio, che eseguono il taglio TE senza tener conto della filettatura della vite o della posizione di fine corsa.
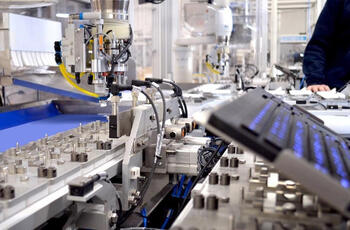
Per supportare i produttori di tappi e chiusure tethered innovativi, Gefit ha messo a punto anche un banco di prova dedicato al taglio orientato, facilmente adattabile e riattrezzabile per diverse tipologie di chiusure e profili di taglio.
Tra le novità proposte dal costruttore, disponibile a richiesta su ogni macchina di assemblaggio e stampo, rientra Gefdata, un'applicazione basata sul web sviluppata per visualizzare i dati di produzione direttamente su PC, smartphone o tablet tramite ID e password. L'interfaccia di Gefdata consente verifiche tempestive e analitiche e rende disponibili una notevole quantità di dati sia nel breve che nel lungo periodo, quali, per esempio, dettagli di produzione, analisi degli scarti, allarmi, consumi energetici e di materiale, interventi di manutenzione ecc.

Nuovi anche gli “smart mould” progettati per essere completamente conformi ai requisiti richiesti dall’Industria 4.0: l’applicazione di micrometri, accelerometri triassiali, sensori laser di posizionamento e di allineamento, sensori digitali di pressione e di temperatura, posizionati in punti strategici all’interno dello stampo e collegati a un software per la gestione e la registrazione dei dati, permette di aumentare non solo la qualità e la quantità produttiva degli stampi, ma la vita stessa dell’impianto, con il relativo crollo dei costi dovuti a interventi imprevisti di manutenzione.
Il lavoro in parallelo dei sensori mantiene l'intero processo sempre sotto controllo, dalla temperatura alla pressione, dall'allineamento tra la parte calda e parte fredda dello stampo a ogni singolo movimento di espulsione. In questo modo vengono monitorate le varie fasi di stampaggio, tra cui il conteggio automatico delle stampate e del tempo di ciclo, registrando le informazioni in caso di non conformità sulla base di precisi parametri preimpostati. Altre caratteristiche aggiuntive prevedono sistemi di controllo da remoto, come sulle macchine di assemblaggio e il monitoraggio continuo dei processi.