Membrana bugnata in HDPE per l’edilizia
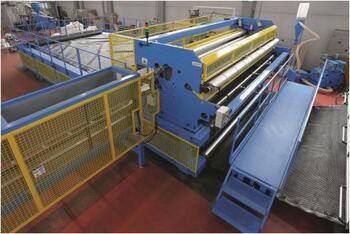
Una linea per l’estrusione di membrana bugnata in HDPE, con larghezza netta di 4 metri, è stata recentemente realizzata da Amut per un importante produttore russo di materiali per l’edilizia. La membrana bugnata in HDPE viene largamente utilizzata per la protezione e il drenaggio dei muri interrati e per la protezione e la ventilazione del manto di impermeabilizzazione tra la fondazione in cemento e il terreno. La sua versatilità, inoltre, la rende idonea alla realizzazione di opere in zone con un’alta presenza di acqua.
L’impianto ha una produttività superiore a 1700 kg/ora e consente di realizzare prodotti in fascia unica da 4000 mm oppure con taglio centrale, per ottenere due bobine da 2000 mm o, in alternativa, quattro bobine da 1000 mm l’una, con un diametro massimo di 490 mm. La velocità lineare cinematica è pari a 12,5 metri al minuto, mentre la gamma di spessori varia da 350 a 1000 g al metro quadro.
La linea si basa su un estrusore monovite modello EA 180 con L/D pari a 45 ed è in grado di produrre partendo da materiale in granuli, in scaglie/macinato o da bottiglie in HDPE post consumo, garantendo un’omogenea alimentazione anche utilizzando materie prime di
diversa granulometria. È composta da: sistema di caricamento; dosaggio delle materie prime, estrusore monovite con capacità di plastificazione superiore a 1800 kg/ora, dotato di degasaggio a vuoto spinto per l’estrazione dei componenti volatili nel caso della lavorazione di materiale da bottiglie post consumo; cambiafiltro in continuo di dimensioni maggiorate; pompa a ingranaggi ad alta pressione, in grado di trattare anche polimeri ad alto peso molecolare; testa piana con una larghezza di uscita della massa fusa superiore a 4300 mm e, quindi, idonea a produrre la larghezza massima anche nel caso di prodotti fini con ridotto spessore (inferiore a 300 g al metro quadro). Inoltre, è presente un gruppo speciale di calandratura/formatura, risultato dell’esperienza del costruttore novarese nel campo della termoformatura. Una tale larghezza, unita alla velocità lineare che doveva essere raggiunta, pari a 10 m/min di prodotto finito, infatti, ha imposto un accurato studio dei flussi di raffreddamento dei due cilindri principali di formatura, tramite pompe di ricircolo-termoregolazione nonché di un sistema di distribuzione del vuoto di formatura in grado di soddisfare le diverse esigenze legate alle tipologie di prodotto finito da realizzare.
Poiché la linea è in grado di lavorare il 100% di materiale da post consumo, anche il gruppo generazione vuoto ha dovuto essere realizzato con sistemi di condensazione/abbattimento del condensato potenzialmente presente a livello di inquinante nel materiale fuso e certamente elemento problematico nel circuito del vuoto. A valle dell’unità di calandratura/formatura è installato un gruppo di svolgimento/accoppiamento di materiali geotessili da 4 metri di larghezza, completo di gruppo di distribuzione di colle “hot melt” per l’adesione di tipologie diverse di materiali di supporto/rinforzo. Il fine linea è composto da un avvolgitore automatico completo di piano di scarico/accumulo delle bobine di prodotto finito.
L’impianto è inoltre dotato di apparecchiature complementari e accessorie quali un gruppo di svolgimento bilaterale di bandella segnaletico/pubblicitaria direttamente applicata in fase di formatura e un gruppo di mulino macina sfridi completo di gruppo di trasporto del materiale macinato direttamente nella zona di carico/miscelazione delle materie prime. Un software proprietario sviluppato e messo a punto in modo specifico per le particolari esigenze della linea, comanda e controlla tutte le funzioni e i parametri operativi, con relativa memorizzazione e monitoraggio del processo produttivo.