Oltre 500 componenti stampati in 3D per la Lotus 62-2
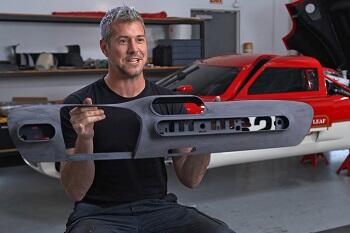
Il produttore di soluzioni per la stampa 3D a base di polimeri Stratasys ha collaborato con il marchio automobilistico di lusso Radford per stampare in 3D oltre 500 componenti per il lancio della Lotus Type 62-2. La costruzione di questa supercar in stile retro-moderno ha offerto il palcoscenico ideale per l'impiego delle avanzate tecnologie della stampa 3D, dalla progettazione alla prototipazione, dall'attrezzaggio alla fabbricazione di parti di produzione utilizzando le tecnologie FDM, PolyJet e stereolitografia di Stratasys.
Per produrre i primi due esemplare della 62-2 sono state stampate in 3D più di 500 parti presso il Radford Studio, la società di design e ingegneria automobilistica Aria Group e il centro di Direct Manufacturing di Stratasys. Utilizzando il software di gestione del processo del GrabCAD Shop di Stratasys, il team Radford ha pianificato e monitorato la stampa 3D in cinque sedi in tutto il mondo, utilizzando contemporaneamente una flotta di 20 stampanti Stratasys dei modelli F900, F770, Fortus 450mc, F370 e J55, utilizzati per ottenere risultati diversi per ciascun pezzo.
"Integrando la tecnologia di stampa 3D all'interno dei suoi laboratori, la Radford è stata in grado di trasportare la produzione di supercar ispirata agli Anni Sessante nel XXI secolo, con lo stile e le caratteristiche di fascia alta estremamente personalizzate che i clienti si aspettano da un veicolo di questo livello. È un esempio straordinario di un fenomeno a cui assistiamo ogni giorno nel settore automobilistico. Chiunque investe in nuovi veicoli desidera un maggiore livello di personalizzazione e la stampa 3D contribuisce a renderlo possibile", ha dichiarato Pat Carey, vicepresidente esecutivo per la crescita strategica di Stratasys.
Utilizzando una serie di tecnologie e stampanti 3D diverse, il team è stato in grado di produrre parti come il grande e solido nucleo del parafiamma a sandwich in materiale composito, realizzato in due metà sulla stampante F900 con resina Ultem 1010. Le due parti sono state poi assemblate per formare un pezzo unico, che è stato avvolto in fibra di carbonio senza l'uso di uno strumento di stratificazione. Il design del parafiamma includeva complessi elementi di montaggio per gli altoparlanti interni, un supporto per il bocchettone del serbatoio del carburante e il vano bagagli. Inoltre, molti elementi esterni come la scocca degli specchietti laterali, i condotti del radiatore e le prese d'aria della carrozzeria sono stati stampati in PA 12 rinforzato e ASA, mentre molte delle staffe di montaggio su tutta l'auto sono state stampate in PA 12 rinforzato, tutti mediante tecnologia FDM in funzione di una serie di fattori, tra cui resistenza, ridotta tempistica del progetto e totale libertà di progettazione.