The anniversary press for a century of Arburg
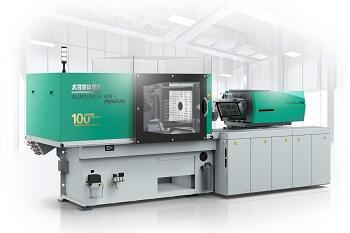
The 100-year anniversary of the Hehl family company has set the stage for Arburg's latest piece of machine technology, the hybrid Allrounder 470 H. This anniversary machine delivers an impressive performance across the board: it saves energy, conserves resources, is production-efficient, user-friendly and reliable all at the same time. The perfect combination of electric clamping unit and hydraulic injection unit significantly reduces acquisition and operating costs as well as the carbon footprint. With Comfort, Premium and Ultimate performance variants, various injection units and a wide range of options, the new Allrounder 470 H machines can not only be precisely adapted to specific customer requirements - they also mark the start of a new generation of machines from Arburg.
"Electric drives are becoming increasingly important, not least in terms of energy efficiency," pointed out Gerhard Böhm, Managing Director Sales and Service. "In the new Allrounder 470 H, we have created precisely the hybrid machine that users need today and in the future; a machine that has not yet been available on the market in this form." The anniversary machine is particularly interesting to customers who are looking for an energy-saving alternative to hydraulic machines, for example, but who also want to benefit from their proven benefits. "The new generation of machines incorporates many technical innovations that are only available from Arburg," added Guido Frohnhaus, Managing Director Technology & Engineering. "When designing the new Allrounder 470 H, we significantly enhanced our proven technology to optimise the energy footprint and reduce cycle times." Contributing factors include the new oil management concept for which a patent is now pending, flow rate splitting for simultaneous movements of hydraulic secondary axes and the extended use of the Arburg servo hydraulic system.
Compared to a similar hydraulic machine, the energy footprint of the Allrounder 470 H is up to 50 per cent better, and depending on the application, up to 12,000 kilogram of CO2 can be saved each year. The new oil management concept also helps to conserve resources: For one thing, around 35% less oil is needed, and for another, waste machine heat is used to pre-heat the oil. In addition, the required cooling water capacity is also between 50 and 70% lower. A reduction in the dry cycle time of up to 33% results in significantly greater production efficiency.
The new oil management concept with improved oil container, differential pressure-enabled oil filter housing and predictive maintenance for filter changes and oil pump inspection are aspects ensuring that the new machines are extremely reliable and operate with low energy and resource requirements. The warning message for a dirty filter is issued when the level reaches 75%, which is early enough to enable proactive procurement of a new filter in good time. Result: no machine standstill. By attaching the filter element to the removable cover with a handle and making the filter housing easily accessible on the operating side, the machine's designers have also made the filter housing more ergonomic. The new oil management concept reduces energy and cooling water consumption and increases the service life of the individual components, in some cases considerably. Hot, contaminated hydraulic oil is separated from cold, clean hydraulic oil in the oil container. Together with the constantly filtered and cooled return volume and targeted flow guidance, the oil quality is improved with an oil volume that is around 35 per cent lower and the service life of the components is increased, thereby improving machine availability. The waste heat from the machine can be used to pre-heat the oil and does not flow back into the cooling water circuit as residual heat. Splitting the flow rate of the hydraulic pump makes it possible to drive an additional secondary axis at the same time. This technology has a positive effect on production and energy efficiency, particularly with the powerful hybrid Allrounder H machines. The machines consume less energy in total and cycle times are also reduced at the same time. These are two real advantages in combination that the hybrid series can offer over purely hydraulic machines.
The Arburg servo hydraulic system (ASH), which has already proven itself in hydraulic and electric Allrounders, has been integrated in the Allrounder 470 H Comfort and Premium machines. ASH enables particularly energy-efficient and low-emission operation, as the speed-controlled, water-cooled servo motor continuously adjusts the drive system to the actual power requirement. This means, for example, that when the machine stops moving, the pump drive also stops and there are therefore no more idling losses. This saves up to 50 per cent of the energy, especially in processes with long cooling times. At the same time, however, the machine's cooling requirements and noise level are also significantly reduced.
The new Allrounder 470 H machines in the Comfort and Premium performance variants celebrated their world premiere as part of the exclusive anniversary events at Arburg's headquarters in Lossburg on 16 February 2023. The anniversary machines will then be on display live at the Anniversary Days from 8 to 11 March and at a host of Arburg events and trade fairs around the world. The new concept will be gradually implemented for other Allrounders in the hybrid Hidrive series.