Four days dedicated to the extrusion of multilayer films for packaging
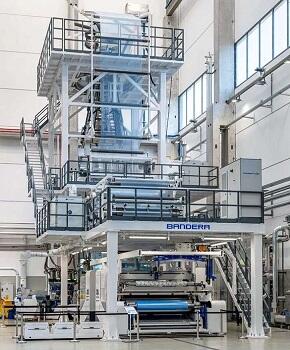
internet website)
From 22 to 26 January, Bandera is opening the doors of its headquarters in Busto Arsizio (Varese, Italy) to introduce the Techno Flex PO5 blown extrusion line for the production of 5-layer film, designed to meet the evolving needs of the packaging industry.
The Techno FleX PO5 boasts a sophisticated configuration aimed at maximizing efficiency and versatility in film production. Its key components include above all the 4 + 4 + 4 + 4 + 4-component gravimetric dosing system, ensuring accurate material dosing and contributing to production quality and consistency. Five extruders of various diameters: a core extruder with a diameter of 85 mm, alongside four extruders with diameters of 65 mm each. This combination provides flexibility in processing a wide range of materials. The 5-layer co-extrusion die head: with a diameter of 300 mm, enables the production of multi-layer films. The Internal Bubble Cooling system (IBC) is managed by a control unit that allows perfect uniformity in film width. The high-efficiency double flow cooling ring is designed for optimal cooling performance. The double flow cooling ring ensures a quick and uniform extrusion of the film.
The automatic film thickness control guarantees precision in film thickness, a critical factor in meeting the specific requirements of diverse packaging applications. The flattening and gusseting devices contribute to the overall quality and appearance of the film, providing the necessary features for different packaging needs. The calibration cages and an oscillating haul-off with a roller width of 1,800 mm ensure accurate film dimensions and stability during the production process. The two-station face-to-face winder: supports contact, gap and combined winding modes, offering versatility in packaging formats. The automatic reel extraction further streamlines the production process. The Trim FleX twin-screw counter rotating system takes care of the in-line recycling of production scrap and rejects. Last but not least, the HMI interface powered by ANY MA offers user-friendly control and monitoring, enhancing operational efficiency.
The line is designed to produce shrink film, lamination film, print film, shrink hood film and general packaging film from a variety of materials, including LDPE, LLDPE, MLLDPE, EVA as well as from MDPE, HDPE and COPP blends, to achieve thicknesses from 20 to 200 microns at an hourly output capacity of up to 450 kg/h.