Performance and Aesthetics in Tecnova’s New Regeneration Plant
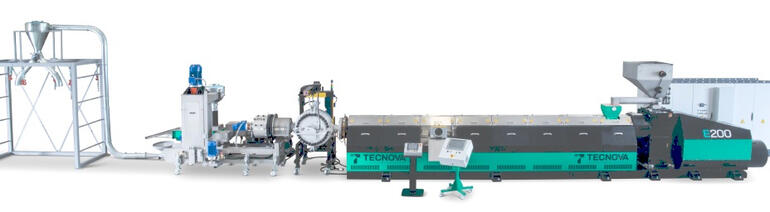
Tecnova's new plastics regeneration system, the E200, has been specifically developed to meet the requirements of a Spanish client for processing post-consumer HDPE, primarily from bottles used for personal and household hygiene products.
In this particular case, the process begins with pre-sorting and washing of the incoming post-consumer material in three connected tanks to ensure the removal of all external contaminants. This step is combined with optical sorting based on colour, to obtain a final product that is as white as possible, in line with the required quality standards.
A key feature of this process is the control and maintenance of the melt flow index of the recycled material within extremely tight tolerances – around ±0.1% of the input value. The system produces a milky white granulate free from impurities, a result also supported by a filtration system below 150 microns, with an optional reduction to 120 microns. This is particularly suitable for applications requiring consistent thickness, such as blow moulding, which is the case here.
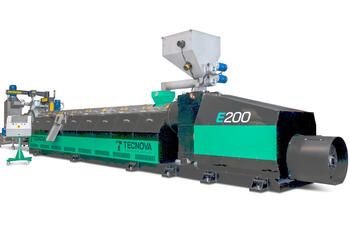
The E200 plant ensures a minimum hourly output of 1,500 kg, a performance successfully tested at Tecnova’s facility in Oleggio (Novara). The system is capable of operating continuously 24/7, an especially valuable feature for components such as the filter, which require several hours to reach operating temperature.
Another innovative aspect of the plant lies in its completely redesigned aesthetics. New guards and coverings give the line a more modern look. Great attention has been paid to both form and volume: a refined design communicates cleanliness, order, and efficiency. This newly styled, fully enclosed machine marks a milestone as the first in a new generation of Tecnova systems. The design also reflects the RAL colours of the company’s recently introduced logo, presented to the market just a few months ago.
The E200 also boasts an impressive level of energy efficiency. Consumption has been kept below 0.23 kW/kg of material produced, thanks to the screw profile of the extruder and the insulation of the guards and cylinder. These figures were verified during the setup phase, with the client able to continuously monitor the plant’s energy consumption via a G-meter displayed on the control screen.
The E200 system is equipped with an intuitive and user-friendly PDC control panel, which guarantees a high level of automation – at least 90% – minimising operator intervention to supervisory tasks only.