From Exact an extruder for hot recovery
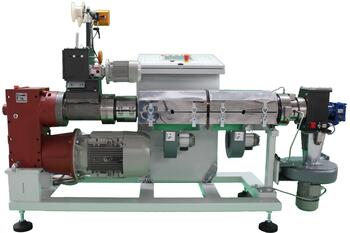
In 2014, Exact is celebrating forty years of activity and, for this occasion, it has launched the new E-15 extruder, which extends its range of product introducing a system for hot recovery. The new extruder is suitable for both closed loop in-line recycling (trimmings of thermoplastic films such as LDPE, LLDPE, mLLDPE, HDPE and EVA as well as barrier films containing COPA and EVOH) and off-line recycling (scrap film reels), and is equipped with a conveyor and a feeding unit for the trimmings with a haul-off equipped with two motorised rollers positioned above the extruder mouth, a solution which avoids the implementation of expensive and noisy Venturi devices.
The granule thus obtained is air-cooled through a spiral conveyor of about 10 linear meters, is homogeneous and has an apparent specific weight similar to that of the virgin granule which can be easily modified by varying the cutting speed. The design of the screw has been specifically developed to turn the trimmings into granules without generating excessive heat. In fact, the screw reaches the melting temperature in a gradual manner, thus avoiding product degradation over the heating cycle. The output of this extruder amounts from 5 to 75 kg/h at a maximum throughput speed of 200 m/min.
The main components of the system include a haul-off unit equipped with high-strength nip rollers, capable of compacting the trimmings and eliminating the screw pulses. Moreover, the machine features a speed follower provided with a rocker roll which balances the speed difference between the line and the haul-off unit up to a maximum of 10%, so as to keep always in tension the trimmings coming from the winder. A sensor detects possible lack of material and stops the extruder screw, allowing it to restart only when the trimmings feeding unit resumes its normal operation. The conveyor grants consistent material flow for the screw, and the trimmings are introduced from above through guide pulleys. The line has three temperature control zones, two of which enable a double function (heating and cooling).
The high-strength nitrided extrusion screw can process a wide range of materials thanks to its innovative profile. The fluidity of the material is actually controlled by a pressure transducer. A rupture disc positioned at the end of the screw protects the die from any overpressure that could damage it, while the die-face cutter can be configured with two or four rotating knives. High quality components, including Omron drives and touchscreens, Siemens electric motors, screw and spindles supplied by leading manufactures in their respective fields round off the extruder’s equipment.