Advanced rotational moulding reduces production costs
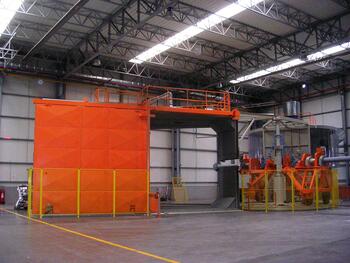
Excluding raw materials, the most significant costs in rotational moulding are labour (approx 55% of total costs), energy (22%) and technical obsolescence (19%). In response to this assessment, Polivinil Rotomachinery continues to invest in research & development, because the most advanced markets, those recognizing the added value of its technologies, express the need to reduce the above costs within a perspective of continuing improvement of production process and product quality.
Reducing labour costs means both decreasing the number of hours of work per unit produced and making machine operation as simple as possible, limiting the need for highly skilled people. The manufacturer does not merely provide machines, but also proposes customized solutions to the converter for enhancing the efficiency of its production process in terms of mould handling, production facility layout, and handling of raw materials and finished products.
It recently released new software that resides on its servers which, given the weight, shape and centre of gravity of the moulds, provides a readily comprehensible diagram of the arrangement of the moulds on the carousel with straight-arm mould holders and on the flange of offset arms to ensure that the load is balanced. Using the PC and the mouse, the production director can move the moulds while the program displays any imbalances in real time, specifying how much and where weight must be added. This is all accomplished without pauses in production, offering clear advantages in terms of mechanical stress and wear of moving parts.
As regards energy savings, Polivinil provides systems where the quality of the insulation and the optimization of the oven profile in terms of speed and pressure of hot air flow over the mould provide up to 20% energy savings for a given cycle time, as well as significant reductions in cycle time for given energy consumption. A further forward step was achieved with the implementation of the Upper Fan Duct (UFD) system, which redirects a portion of the hot air still at operating temperature back over the mould. Practically speaking, it is a supplementary heating point obtained from the same heating unit with no increase in energy consumption. A new type of blower fan was also introduced with twin turbines that quickly reach optimal rotation speed and also slow down quickly, significantly reducing heat loss from the oven when the doors are opened. The greatest advantage is achieved in combination with Ecomode, where the burner is shut off when the oven doors are open and the fume extraction flow is minimized.
As regards energy for motors, in addition to the Regen system, which recovers energy via inverters that convert DC to AC when the motors decelerate or reverse rotation and act as generators, special air/air and air/water heat exchangers are also being developed to use heat generated in the production process to heat interior spaces and also tap/shower water.
The integrated control software manages all the above and, on the basis of moulding temperature and mould cooling profile, measured in real time by sensors in the mould, regulates the duration and sequence of production phases. According to settings dictated by the supervisor, as soon as the internal mould temperature reaches the set value, the mould-holder arm is ready at the exit from the oven. The same thing happens in the cooling phase: when the material detaches from the mould walls, the software asks the operator to ok mould removal, extraction of piece and loading of material for the subsequent cycle. The advantages are seen when material quantity or type changes, for the first cycle of the day (cold oven), and in summer/winter cooling, with the cycle adjusting automatically to changing production conditions.
The reduction in machine cycle times is also achieved by improvements in the cooling phase. The objective was reached by the use of fans that are both more powerful (going from 28,000 to 40,000 cubic metres/hour, each) and quieter (by 10 dB), and that require half the amount of electricity. Savings are displayed in real time on the monitor: electricity and gas consumption may be organized by work cycle, arm, cubic metres, kg of product or intermediate times.