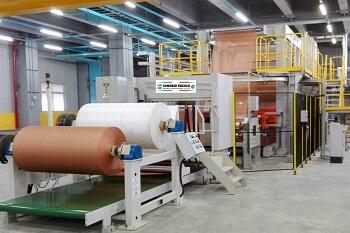
A leading Italian engineering and manufacturing company, Comerio Ercole has recently signed an exclusive agreement for rubber calendering process with Herrmann Ultraschaltechnik to pursue joint cooperation for a very innovative technology for the production of carcasses in the rubber calendering field where a tail and head of fabric cords is considered in term of lamination between the two materials. The innovative joining system has been named Ultrasplice and the development work involved the bonding of textile fibres which serve as inserts for the carcasses using ultrasound technology.
"When our long-standing partner Comerio Ercole approached us with the idea, we quickly realized that ultrasonics could be used to bring real added value for the customer. Together, we succeeded in developing a solution that makes the cord splicing process even faster and more efficient. In addition, the connection is stronger and more stable, which makes the process safer. For the end customer, the newly developed process results not only in faster cycle times but also in enormous savings potential for the machine construction", says Christoph Ochs, key account manager at Herrmann Ultraschall.
“The traditional technology is linked to the minimal time to vulcanize into heated splice press the rubber splice joining the tail with the head of the new fabric bobbin, this process requires around 30-40 seconds. With Ultrasplice the welding process between tail and head is obtained in 2-2.5 seconds. The ultrasonic welding operation is performed in less than 1 second. In the total time of welding process is it necessary to consider also the lowering and lifting of the actuators, that require around 1.5 seconds. In addition no rubber splice is no more present in the product avoiding any specific problem may usually arise during calendering process, including thickness gauge critical impact. Our R&D team is very proud about the fruitful cooperation with Herrmann group” says Mario Sacchi, R&D tire director at Comerio Ercole.
Thanks to the ultrasonic technology, the splicing time is dramatically reduced, therefore the capacity of the pre-calender accumulator is reduced. The innovative splice press is manufactured by Comerio Ercole while the tailor-made ultrasonic actuators are provided by Herrmann. The continuous processing of materials requires a perfect synergism between system components and technologies: the exclusive cooperation between the two companies for rubber calendering process filed allows to develop customized solution from the design to the customer services support.
The technological concept is based on high-frequency sound waves that cannot be heard. Ultrasonic welding uses frequencies around 20 kHz which are perceived as vibrations. When the ultrasonic vibrations hit a thermoplastic material, the molecular chains start to oscillate, and the molecules start to move and rub against each other. This generates energy, referred to as friction heat. In the case of thermoplastic materials, this process causes them to start to melt. Ultrasonic welding takes advantage of this principle and after a short hold time under additional pressure, materials can be welded together at a molecular level in the joining area.